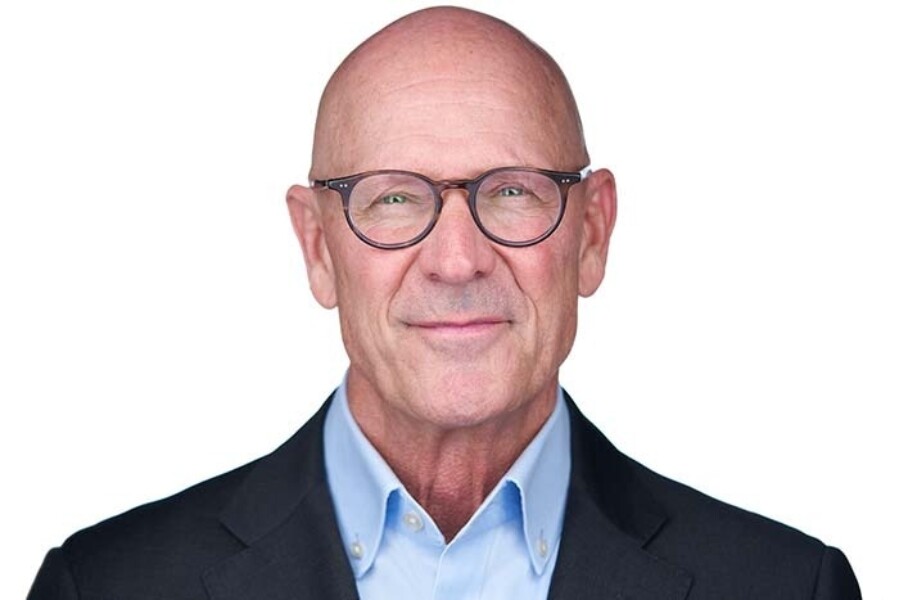
When it comes to achieving success in business, specifically in manufacturing, agility is key. During my time at Southwire, our team has worked to meet various challenges as the company grows. One of the most significant ways we do that is by leveraging SAP to hurdle new obstacles while refining our efforts in production and delivery.
Our company is one of North America’s largest wire and cable producers and an emerging influencer in many important electrical markets. Southwire and its subsidiaries manufacture building wire and cable, metal-clad cable, utility products, portable and electronic cord products, OEM wire products, and engineered products. In addition, we supply assembled products, contractor equipment, and hand tools.
Creative Means, Significant Investments
Since joining Southwire as SVP and CIO, I’ve been focused on digital transformation across our organization’s footprint. We’ve used some creative means to accomplish this, such as installing modernized manufacturing equipment and developing plans to implement additional features that will track everything from production to shipping and delivery. All of this involves significant investments into our Operational Technology (OT) and Information Technology (IT) infrastructure.
Our company has experienced great success over the last three years. The efforts we are making in the modernization of our factories have opened the doors to improving our operations. When we step back and look at the bigger picture, leveraging our company’s SAP systems is at the core of Southwire’s digital transformation.
Our approach to the challenges associated with analyzing and improving manufacturing processes revolves around our overall goal of continuous improvement. In the last few years, the company has been recognized and awarded for our efforts related to sustainability, developing innovative systems and solutions, exercising environmental stewardship, and enhancing the well-being of our communities through the core tenets of Growing Green, Living Well, Giving Back, Doing Right, and Building Worth. We also have employee resource groups (ERGs) that work with various parts of our team to continually build a more diverse, equitable, and inclusive culture.
No Small Feat
This modernization effort is no small feat. We’re committed to a multi-year plan to integrate newer and better equipment, systems, automation, and technology. We aim to transform all our operations, increase efficiency, enhance Southwire’s competitiveness, and ensure operational capability and capacity to support strategic growth.
Our digital transformation focuses on improving the customer experience, automating manual processes, and improving business processes throughout the organization.
All these efforts and changes bring with them the need to modernize our organization’s IT personnel. We began moving our SAP environment to the Google Cloud Platform in 2020, where we started modernizing Southwire’s infrastructure. Doing this helped us make sure our company had a platform to move quickly with scalability, flexibility, and security. Since then, we’ve moved most of our tier-one applications to the cloud. We strive to eliminate much of the old infrastructure that sometimes comes with a growing manufacturing organization.
Any new manufacturing shop floor equipment and machines will be connected to our network as part of IoT. We will leverage technology to capture and collect data on every process within our operations. This creates a large opportunity for our team to analyze what’s really happening on the shop floor side and begin to look at ways we can potentially improve those operations through AI and machine learning.
Southwire’s goals include the ability to closely monitor orders at any time in the operation process of our manufacturing facilities. As we do a better job tracking orders from end-to-end, we will do a better job sharing that information with our customers so they know when to expect the products. This is all part of Southwire’s goal to improve our customer experience.
New World
Looking ahead, we will be interested in bringing in talent related to AI, machine learning, robotic process automation (RPA), data scientists, and a range of other areas. The technologies that we currently have, and the addition of new technologies, will all strengthen our core. We must become a technology company as much as we are a manufacturing company. The two really go together in a new world when you consider the newer equipment we are installing.
Not only are we expanding into new and exciting areas of operations, but Southwire is also establishing new locations that expand our presence, giving us a competitive edge for talent recruitment and retention. We’re excited to have opened our new office space at The Battery Atlanta in Cobb County adjacent to Truist Park, home of the Atlanta Braves, last month.
When I think of where Southwire is going, and this may sound cliché, the future truly is now. We have already started the digital transformation and modernization journey, making it an exciting time to be at Southwire.
Dan Stuart is Southwire Senior Vice President and CIO and an ASUG Board Director.