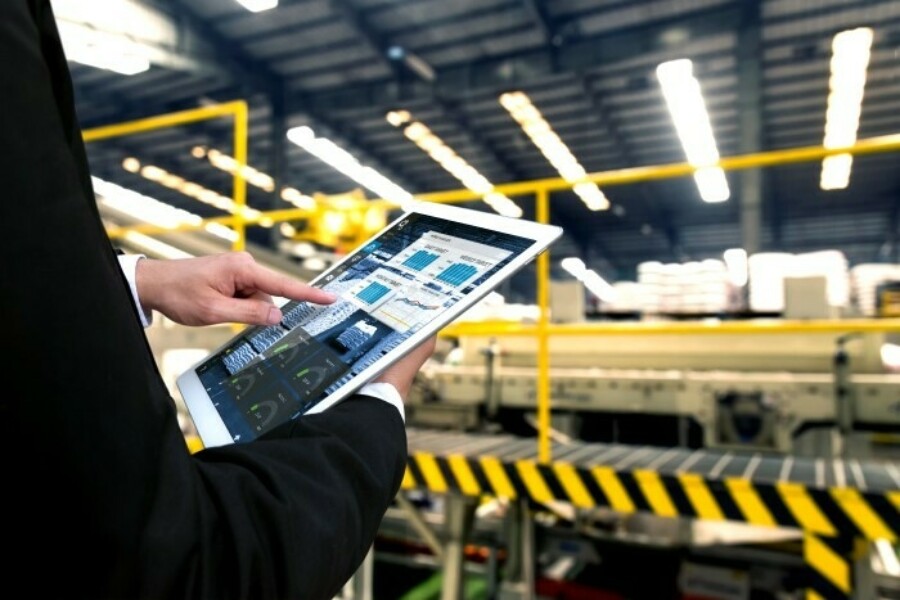
The term “digital economy” has existed for a number of years now as a concept that is meant to empower both consumers and companies to better connect and engage with each other. At the center of that exchange is the supply chain, which keeps goods moving, global economies bustling, and the world turning.
As the business landscape has been reshaped by a global pandemic, this has caused supply chains to either work overtime or come to a screeching halt. Now it is more important than ever for technology to play an essential role in this essential business function.
We spoke to Richard Howells, VP of solution marketing at SAP digital supply chain, about how a digital supply chain powered by Industry 4.0 can help organizations overcome challenges and prepare for the future. “I’ve been at SAP for about 16 years and I’ve worked in the supply chain and manufacturing industries for about 30 years,” he said. “There’ll always be a challenge to overcome, but intelligence makes it easier to deal with.”
Sharon: Can you give us a high-level overview of what a digital supply chain is?
Richard: First, a digital supply chain is connected. That means it’s connecting people within your organization and connecting companies within your network so that you can collaborate across customers, suppliers, contract manufacturers, logistics, providers, and so on.
Second, a digital supply chain is automated. We now have access to technologies such as the Internet of Things (IoT), machine learning, and artificial intelligence (AI), and this provides access to real-time data across the supply chain. It helps companies leverage that information to drive agility and resiliency across the supply chain.
And third, a digital supply chain is intelligent. With information and intelligence, you have visibility across the end-to-end supply chain, which means you’re able to predict things that will happen. I can predict when a machine in my production line will go out of calibration and may need to be maintained. I can predict the quality of products and make changes during production if necessary. I can predict where vehicles are and if they’ll be on time or late based on traffic patterns. And I can also predict whether the goods in that vehicle are of good quality.
All those things—connection, automation, and intelligence—are part of digital supply chains. The supply chain fits in after the full product life cycle, from design through manufacturing and logistics, to their operation at customers’ locations. And of course, the related planning processes that span the end-to-end supply chain apply to the digital version too.
Sharon: What are some of the challenges supply chains are facing today and how would a digital supply chain help address those issues?
Richard: Today is much different than four months ago. We’re seeing a very unstable supply of raw material and intermediate, as well as finished products, as manufacturing and borders shut down and start to reopen.
At the start of the pandemic, we saw a lot of volatile demand for vital commodities such as bread, milk, eggs, hand sanitizer, and toilet paper. They weren’t in the stores, or, if they were, they were at marked-up prices and available in limited quantities. At the same time, nobody was buying luxury products or discretionary items, and their demand dropped off. Volatile demand—whether that’s increased or decreased demand—is a supply chain challenge.
We also had constraints regarding logistics capacity and the actual workforce being able to go to work. Even as facilities begin to reopen, it’s in a different world where the health and safety of everyone in the supply chain are top of mind for companies. This translates to a reduced number of employees in a factory or a warehouse, and more money spent to install plexiglass shields to separate workers. It means more cleaning in between shifts, as well as other measures. All of this has increased the need for improved planning, scheduling, and environmental, health, and safety (EHS) processes.
Both of these challenges can be addressed with a digital supply chain, which would provide the visibility and data to make informed decisions. A digital twin, for instance, would allow a company to do simulations to see how what-if scenarios would help mitigate these challenges.
Sharon: Let’s talk more about digital twins. How can they help a company mitigate risk to products and brands, as well as employees, during these unprecedented times?
Richard: Let’s start by defining digital twin, which is a digital representation of a physical thing, an area, or a process. It could be a digital twin of a piece of equipment, a production line, or an entire factory. It could even be a twin of your supply chain. The key is having visibility through a digital representation at your fingertips.
What we’re seeing is, as the cost of sensors continue to come down, it is more affordable to put intelligence into everything. And once we start getting smart products and assets throughout the supply chain, then you get what we call a digital thread of that product throughout its life cycle—all the way from the time it’s designed through manufacturing, through usage with customers, through ultimately the decommission of that product in a sustainable environment. This could improve lots of things across the design-to-operate process. You can improve performance, engineering, and visibility at any point in time. And a digital twin can also drive new business models and improve customer service.
Sharon: What is the Industry 4.Now initiative at SAP and how will it play into continued innovation within supply chains?
Richard: Industry 4.0 has been around for a while. It started in Germany about a decade ago, and depending on where you are in the world, it might have a slightly different name. But ultimately, it is about an industrial revolution and the automation of business. It started with smart manufacturing initiatives where we were putting sensors on the production line, but it’s more than that now.
I mentioned earlier the cost of sensors coming down, and that has led to developing smarter products and assets. Those intelligent “things” are proliferating across the supply chain. That gives us the opportunity to move Industry 4.0 from a factory-focused initiative to a companywide supply chain business strategy to drive productivity. It’s about leveraging that data across the supply chain to make smarter decisions, to be more predictive, to be more intelligent, and to empower people.
Industry 4.Now is an SAP initiative where we’re talking about Industry 4.0 as an engine for productivity. Because SAP can leverage the intelligence and data from sensors all over the supply chain, it believes the time for Industry 4.0 is now, that the technology is ready, that companies are ready, and SAP is ready.
Sharon: What steps does a company need to take to become a digital supply chain? What’s required to get there?
Richard: There are three different things to focus on, starting with putting the customer at the center of your business. Customer-centric business processes were valuable pre-pandemic, critical during the pandemic, and will be a differentiator post-pandemic. As the situation has highlighted, if you don’t have an accurate view of actual demand, all other processes across the supply chain are working based on bad information.
As consumers, we have focused less on luxury items and more on necessities, which has caused a very volatile demand picture. We have thought less about personalized products and more about personal safety, which in turn means we care less about a great shopping experience and more about a great delivery experience to our front door. And we were not thinking in terms of “one-day delivery” but more about delivering as promised. But forward-thinking companies know that post-pandemic, we will again see the rise in personalization of goods. These companies will continue designing, manufacturing, and delivering products in a more sustainable manner, ultimately becoming more customer-centric.
The next part is to ensure visibility across the network. This is critical because in today’s business, most companies focus on their core competencies and outsource the rest. We rely on a network of suppliers, logistics service providers, contract manufacturers, and other trading partners. Having the right information in the hands of the right people, at the right time, and at the right level of detail is key to respond to shifting conditions, minimize risk, and identify opportunities. This requires data from processes, people, trading partners, products, and assets to deliver an integrated end-to-end digital twin of your supply network. This is what is needed to drive advanced decision-making and predictive analytics all the way from design to full-scale deployment and operations.
The third area is to improve productivity through automation, and this is where Industry 4.0 plays a vital role.
Sharon: What are some of the trends/lessons learned that you’re seeing coming out of a COVID-19 business landscape as it relates to the supply chain?
Richard: One of the lessons learned is that we need to balance cost and risk. Over the past 10 to 15 years, everything has been outsourced because it was cheaper to make it somewhere cheaper. COVID-19 showed us the inherent risk this could bring. When China, which has a huge percentage of goods going through it, shut down, so did many supply chains. So, we know that we need to think about alternate sourcing strategies as a key risk-mitigation strategy.
Another lesson is around inventory optimization and planning. I think some companies will move from “just-in-time” manufacturing to a “just-in-case” strategy. Inventory optimization means keeping the right inventory at the right quantity at the right place in the supply chain. For example, keeping key components and parts close to the manufacturing facility. We’re seeing lots of pop-up warehouses appearing at different companies for that very reason, to hold the inventory closer to where it’s needed.
And the last lesson learned is that supply chains need to be much more resilient. That partly means having risk strategies in place, but also having the ability to take action when something happens. It’s the ability to sense—or, even better, predict—when something’s going to happen, but also be able to respond to it in a timely manner.
Sharon: What are three predictions you can make about supply chains and technology in a post-COVID-19 world?
Richard: I predict that supply chains will become more resilient. They are all now operating in the new normal and must be able to respond to change.
The second is sustainability. It was a huge issue pre-pandemic, and it has not gone away. Unfortunately, and rightly so, it has taken a back seat in the past few months because, quite frankly, we’ve had much bigger short-term challenges to take care of. But the reality is that the pandemic has actually had positive impacts from a sustainability standpoint. It has shown that we can make a difference when we reduce manufacturing or transportation emissions. We’ve seen the air quality improve. I read recently that the Centre for Research on Energy and Clean Air reported that carbon dioxide emissions in China reduced by 25%. That just shows that we can make a difference, and so I believe sustainability will be huge moving forward.
And the third prediction is that the supply chain will have a seat at the table in the boardroom. It is practically a presidential topic at the moment, and I don’t think I’ve heard the supply chain mentioned as much as it has in just the past few months. Supply chains have long been considered a way of reducing costs, but now I believe we have to balance the cost and risk continuum. I also think that with all of the data now available across the supply chain, supply chains will also become an area of business innovation and revenue growth.
Sharon: What would you like ASUG members to know?
Richard: I think supply chains have been critical during the response phase of COVID-19, and they will be equally critical in the recovery phase and in helping companies reimagine their businesses moving forward.
Join ASUG on May 11 and 12 for ASUG Best Practices: SAP for Supply Chain. This virtual event will feature customers, experts, and thought leaders discussing how the last year has challenged and changed supply chains, and what technologies companies are using to bolster their supply chains. Register to attend now.