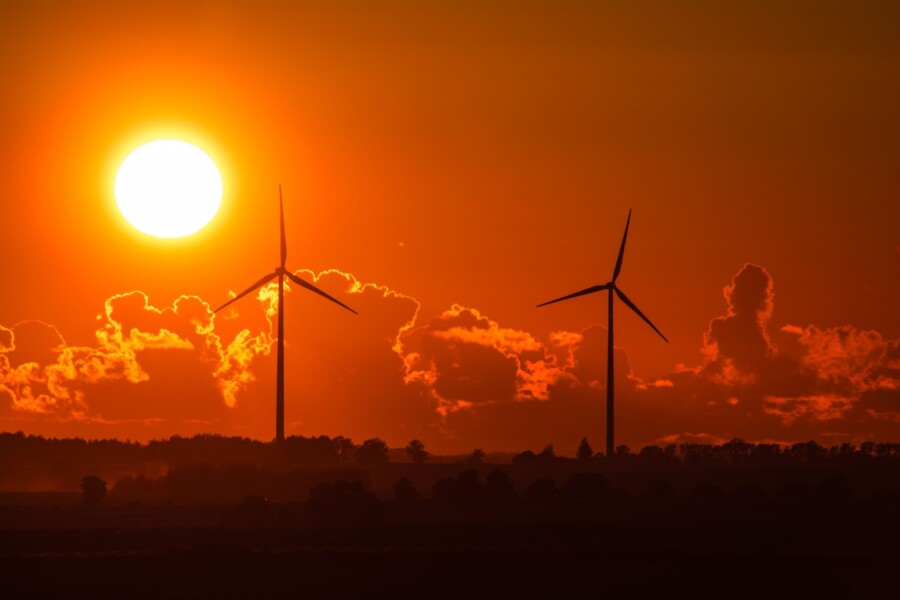
For many businesses, the factory of the future is already here. Robotics, sensors, the Internet of Things (IoT), machine learning, and more are integrated throughout plants everywhere, across industries. And behind this increasingly intelligent industrial world, you’ll also find electronic representational models running parallel with the physical pieces of equipment.
What Exactly Is Digital Twin?
This type of advanced modeling powered by connected sensor data and IoT is known today as “digital twin.” It allows companies to build data-rich models of everything from airplane turbines to escalators and electronic door handles.
Created by software engineers and data scientists with an understanding of mechanical form and function, a digital twin can run concurrently with a physical product to constantly monitor its life cycle. Digital twin can also create simulations that apply artificial intelligence to “learn” how to mirror more realistic or lifelike conditions.
How Digital Twin Empowers Predictive Maintenance
Today, most maintenance happens in response to an actual failure or, at best, it’s preventative and time-based. But how do you know when a part truly needs replacing or a machine requires maintenance? A lot of inefficiencies are bound to happen when enterprises replace the same, perfectly functioning part every 12 months as a part of their regular maintenance cycle.
Now imagine an elevator engineer arriving to fix a fault six hours before it actually occurs. Imagine a rail operator getting a message that a train door will fail to open after 24 more repetitions of opening and closing. Imagine your car sending a specific alert requesting that you take it to the shop to replace the alternator in your engine, a full day before it breaks down. Digital twin makes this type of truly predictive maintenance possible using connected sensors and data analytics.
Virtual Models to Explore the Physical World
Digital twin brings data-driven virtual equivalents together with physical assets to provide real-time, intelligent information to help with decisions. It is an integral part of the Internet of Things (IoT) and an opportunity for us to better understand our world. As we construct smart cities and connected communities, we still need bricks and mortar and steel and concrete, but we can get additional vision from digital twins and IoT-connected smart sensors on everything from traffic lights to lampposts and skyscrapers.
This is where SAP Predictive Engineering Insights comes into context. This cloud-based solution is powered by SAP Leonardo, which began its life as a purely IoT-focused technology platform before expanding its scope to embrace wider enterprise-level software deployments.
How SAP Predictive Engineering Insights Works
Going back to our elevator example, engineers now must perform physical inspections to simply assess wear and tear. But this workload could be dramatically reduced with the help of digital twin. SAP describes how equipment evaluations can be replaced by ongoing, live digital inspections and analysis. Engineers only need to appear on-site when physical remediation, maintenance, or upgrades are truly required.
Now imagine how much this will help enterprises responsible for monitoring millions of miles of pipelines, or for maintaining equipment in remote, hard-to-service locations like offshore oil rigs. You can also see where digital twin simulations could help companies manage the safety of their workers, such as in plants that naturally operate with certain environments that are dangerous for human inspectors.
Based on the form factor and function of the engineering in question, SAP Predictive Engineering Insights can be configured to report on the individually defining factors of the physical items it monitors. The solution combines a standard engineering methodology for calculating forces, stresses, and fatigue based on sensor data, with a high-performance 3-D engine to help you visualize these engineering insights.
Multibody Dynamic Simulation for Your Assets
SAP has built its Predictive Engineering Insights digital twin technology on an code base and tool set obtained from the company’s acquisition of Fedem Technology. This Norwegian company specializes in advanced engineering analysis and building software for “multibody dynamic simulation.” Its expertise lies in the lifetime calculation of structures and mechanical systems under the influence of complex loads, which means it can provide an overview of the structural integrity of a complete asset at any time.
“This solution delivers on our Industry 4.0 vision for a network of digital twins to help our customers predict and improve asset performance and reliability with engineering insights,” said Hans Thalbauer, senior vice president for IoT and Digital Supply Chain, SAP. “We are enabling a virtual network for secure and distributed systems of record, real-time collaboration across the digital supply chain, new business model delivery, and advanced analytics.”
SAP is designing its network of digital twins to synchronize in real time the virtual, physical, conditional, and commercial definitions of assets and products. It is intended to help customers accelerate innovation, optimize operating performance conditions, predict service requirements, reduce risk, improve diagnostics, and make more-informed decisions.
Full-Circle Operations Process Management
The technology is intended to work in an expanding arc that ultimately becomes a virtuous circle. Customers are encouraged to attempt to increase their own operational efficiency by connecting real-time SAP Predictive Engineering Insights to core business processes and other SAP Leonardo-based asset management solutions, including SAP Predictive Maintenance and Service and SAP Asset Intelligence Network.
You could think of this virtuous circle as “Full-Circle Operations Process Management.”
If you’re looking to learn how your peers are doing more
with enterprise asset and supply chain management, join us at the SAP-Centric EAM & Supply Chain conference.