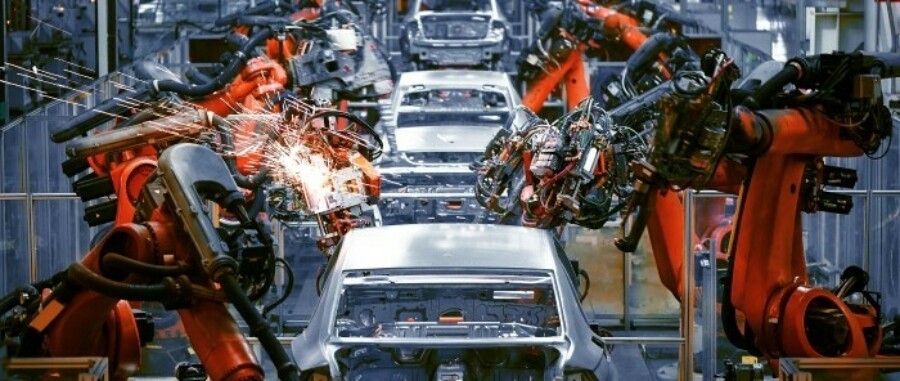
The automotive industry has experienced a series of ups and downs as a result of the COVID-19 pandemic. At the onset, many of the big car manufacturers closed their plants, as the world scrambled to understand the virus. In North America, manufacturers also pivoted from producing cars to making vital PPE (personal protective equipment) for their employees along with local health care workers.
Running these multifaceted operations—especially in complicated times—requires effective technology. Managing crucial supply chains and sourcing materials necessary to construct vehicles (and PPE) requires intuitive, capable solutions to maintain intricate processes. Over the past few months, ASUG caught up with few prominent automotive companies about how technology has allowed them to support their operations now and strengthen them for the future.
Purchasing with SAP Ariba
In an interview with ASUG CEO Geoff Scott at ASUGFORWARD in June, Keith Combs, director of Global Indirect Purchasing at Ford Motor Company, discussed how the company was at the beginning stages of implementing SAP Ariba and SAP Ariba Discovery.
As the director of indirect purchasing, Combs described his role as “responsible for everything we buy that we don’t bolt on to the car.” In the early days of COVID-19, this indirect purchasing was vital to Ford’s output as it began creating a return-to-work strategy. Employees must physically work in Ford plants overseeing the assembly of vehicles and the PPE gear the company began producing. Combs discussed how buying masks, tents, and hand sanitizer became vital for Ford as it began restarting its operations.
His team’s focus became acquiring important materials needed to ensure the safety of Ford’s workplace-dependent workforce as it returned to plants across North America. Part of the problem was that Combs and his team were purchasing items using only guesswork, as opposed to concrete calculations.
“I can’t think of a time ever in my career where we were trying to buy things without a firm demand written down,” Combs said. “It’s been a wild ride. It’s like trying to build a car as you’re driving it.”
Updating Procurement Solutions and Capabilities
Procurement and sourcing materials became particularly tricky as auto manufacturers shut down plants, but still found themselves in contracts where they needed to pay for more materials despite a sizable decrease or complete halt of production.
In another session during ASUGFORWARD, Goodyear Tire & Rubber Company walked attendees through the tire manufacturer’s recent journey to upgrading its procurement solutions. With help from SAP, Goodyear transitioned from the SAP SRM (supplier resource manager) platform to a new tech stack that included SAP Ariba Guided Buying module and the SAP S/4HANA Central Procurement Hub. As SAP announced it will end its support and maintenance of SAP SRM in 2027, Goodyear decided to move to this new solution. It made the decision to transition after the company engaged both its internal stakeholders and internal IT leaders. During the presentation, Saleem Bahezaad, a global business IT partner at Goodyear, walked attendees through the company’s procurement IT road map, which covered its business strategy, technology road maps, prioritizations, and execution plan.
The new solution will give users an intuitive user interface and improved buying compliance. Additionally, SAP S/4HANA for Central Procurement will now support the company’s five regional SAP systems, along with providing centralized management of Goodyear’s global indirect purchasing.
Implementation Assistance from SAP
Goodyear’s journey was aided by SAP through the SAP MaxAttention program. “The SAP MaxAttention program is a multiyear premium support contract that customers leverage to safeguard their projects and operations,” said Rajiv Palkhiwala, chief solution architect at SAP.
Through this program, SAP supported Goodyear’s implementation of its new solutions for the entire life cycle, from discovery all the way to go-live. According to Palkhiwala, the goal is to help companies “transition to the Intelligent Enterprise.” SAP helps companies as they evaluate application architecture, interaction strategies, gap validations, and enablement.
SAP also ensures that a customer’s IT team is completely ready to take over support of the new solution, along with helping prepare a transition plan so companies can monitor important business processes.
Don’t pass up the opportunity to hear from more automotive companies—including both Ford and Goodyear—at our ASUG Best Practices: SAP for Industries virtual event on Sept. 24–25. Register now.